How to create a parallel thread profile with CAD software
In this article, I would like to introduce a typical way to create a parallel thread profile in any CAD software. Parallel threads or straight threads include Metric Screw Thread (M), Unified Inch Screw Thread (UN UNC UNF UNEF), Whitworth Thread (BSW BSF), Miniature Screw Threads (S), Thick Steel Conduit Thread (CTG), and Metric Trapezoidal Thread (Tr). In common, there are five steps to creating a thread profile:
- Step 1: Search for the thread dimensions.
- Step 2: Create the fundamental triangle of the thread.
- Step 3: Create lines for pitch diameter, major diameter, and minor diameter.
- Step 4: Trim away lines to create a basic shape for the thread.
- Step 5: Copy the basic thread form to create multiple thread forms.
Let’s start creating a thread profile for external metric screw thread M6x1 6g. An external metric screw with a thread size of 6 mm, a pitch of 1 mm, and a tolerance class of 6g for both the pitch diameter and the major diameter is used in this example. That’s all the information we have; now proceed as follows:
Step 1: Search for the thread dimension
Go to the Metric Screw Thread (M) page. First of all, we got the thread form angle of 60° from the “Profile” section. Next, scroll down to the “Dimensions” section, enter the specification of thread into required fields: enter 6 into the “Size (mm)” field, enter 1 into the “Pitch” field, select External, and choose 6g for both pitch diameter tolerance class and major diameter tolerance class. Finally, press the “Search” button.
Scroll down to the “result” field to get the result for all dimensions. Here is the result for M6x1 6g. We only use the diameter dimensions.
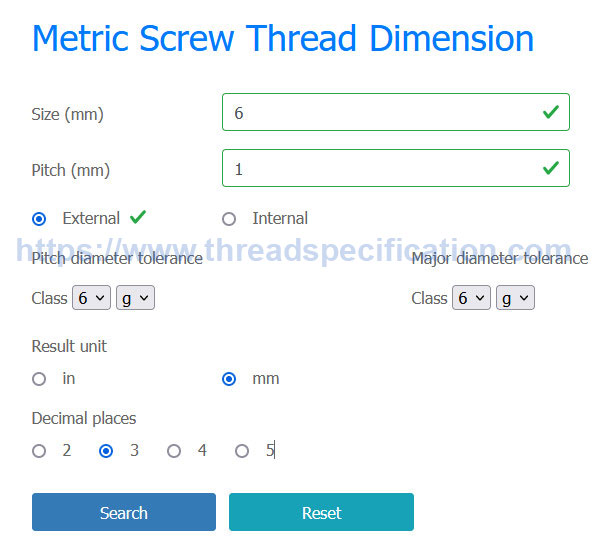
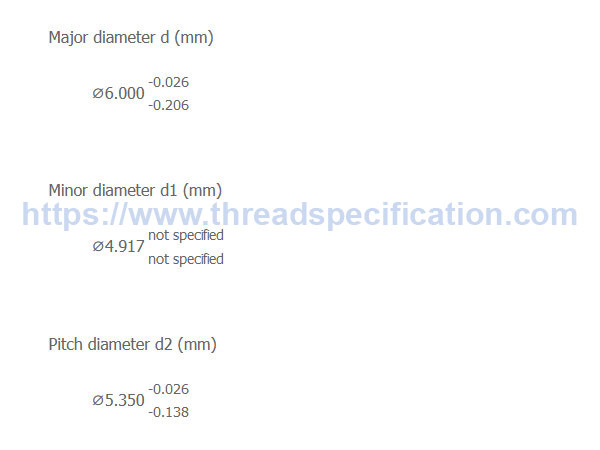
In this case, the tolerance for the minor diameter is not specified because, in machining external thread, the minor diameter is determined by the form of the cutting tool. We can use the tolerance of the pitch diameter for the minor diameter, so the result becomes like this:
Basic diameter value | Upper deviation | Lower deviation | average value |
---|---|---|---|
d = 6 | -0.026 | -0.206 | 5.884 |
d1 = 4.917 | -0.026 | -0.138 | 4.835 |
d2 = 5.35 | -0.026 | -0.138 | 5.268 |
We use the average diameter value to create the thread profile. Now go to step 2.
Step 2: Create the fundamental triangle of the thread
After getting all the diameter dimensions, pitch, and angle of the thread form, we continue to create the fundamental triangle. You can find the definition of the fundamental triangle here.
First, create a horizontal line P1P2 whose length is the pitch of the thread (P1P2 = 1 mm).
From P1, create a line that inclines 60° from the horizontal. The inclined angle is 60° because it is 90° minus half of the thread form angle, which is 90° – 60°/2 = 60°. The length of the line is arbitrary.
From the point P2 we also create a line that inclines 60° from the horizontal. The length of line is arbitrary. Call P3 is the intersection point of two inclined lines from P1 and P2. Trim the unnecessary line, and we have the fundamental triangle of thread.
From P3, create a vertical line that is perpendicular to the P1P2 line. This line is the height of the fundamental triangle. We call the middle of this line P4, which is used to determine the pitch diameter. We finish creating the fundamental triangle of thread. Let’s continue to step 3.
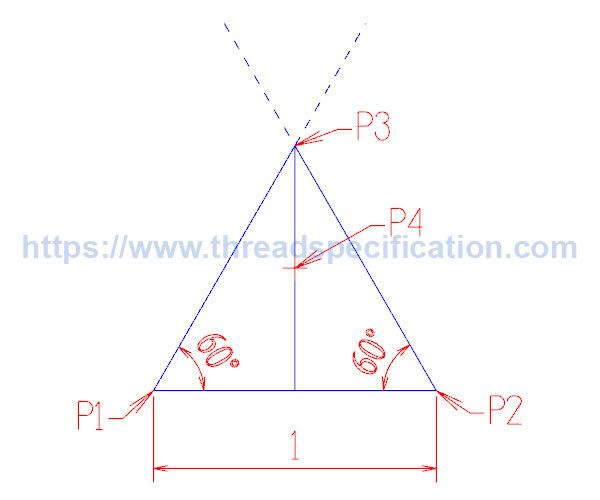
Step 3: Create lines for pitch diameter, major diameter, and minor diameter
First, create a horizontal line anywhere else beside the fundamental triangle. Call this line L1, which stands for the axis of the thread.
Create the second horizontal line that is parallel to L1, on the upper side of L1, and offset from L1 by a distance equal to half of the minor diameter d1 (radius of the minor diameter d1). The distance is 2.4175 mm. Call this line L2, which stands for the minor diameter d1 of the thread.
Create the third horizontal line that is parallel to L1, on the same side as L2, and offset from L1 by a distance equal to half of the pitch diameter d2 (radius of pitch diameter d2). The distance is 2.634 mm. Call this line L3, which stands for the pitch diameter d2 of the thread.
Create the fourth horizontal line that is parallel to L1, on the same side as L2, L3, and offset from L1 by a distance equal to half of the major diameter d (radius of the major diameter d). The distance is 2.942 mm. Call this line L4, which stands for the major diameter d of the thread.
Create a point on L3 (pitch diameter) anywhere that you want; it will be the standard plane for measuring the diameters of thread. We call this point P5. Now move the entire fundamental triangle from point P4 to point P5.
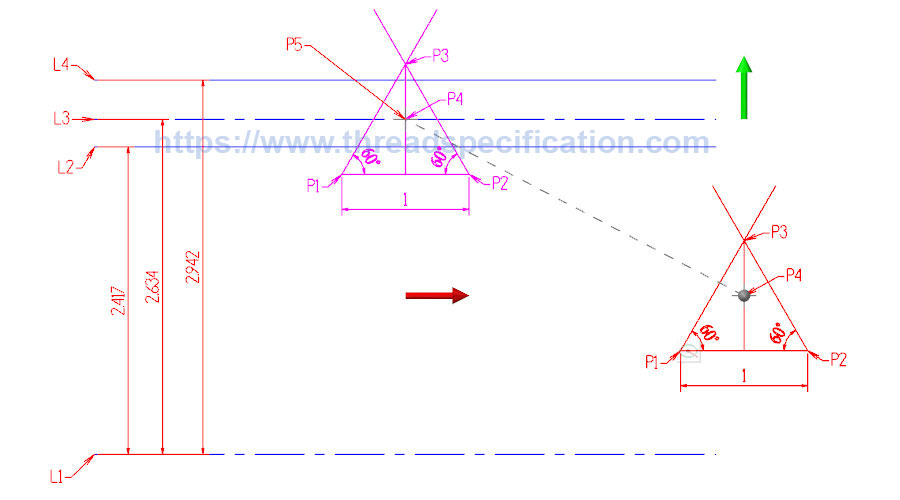
After moving the fundamental triangle to point P5, from point P1 of the fundamental triangle, we create a vertical line that goes through L2. We call P6 the intersection point of L2 and this line. And, from the fundamental triangle’s point P2, we create a vertical line through L2. We call P7 the intersection of L2 and this line. We finish step 3 and go to step 4.
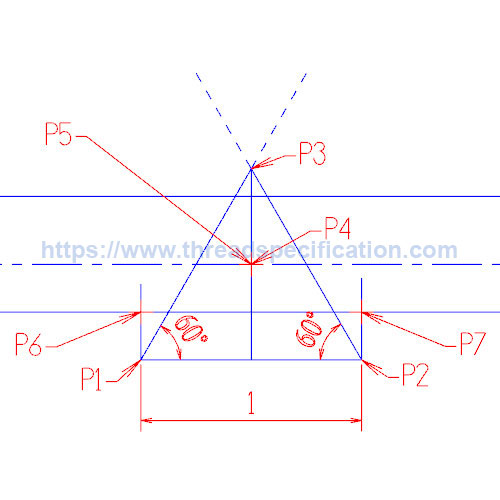
Step 4: Trim away lines to create a basic shape for the thread
Trim away all unnecessary lines, and we get the basic form of thread.
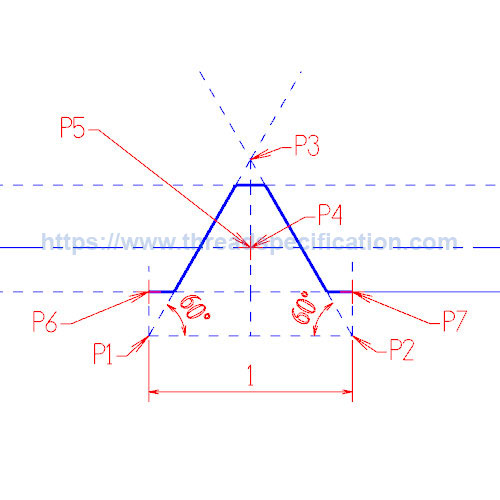
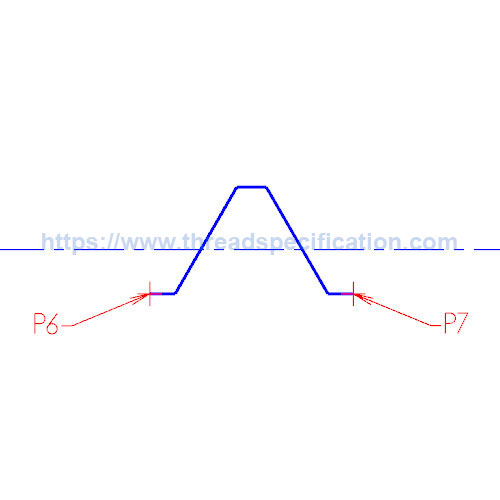
Step 5: Copy the basic thread form to create multiple thread forms
Copy the entire basic thread form from point P6 to point P7 or from point P7 to point P6 to create multiple thread forms. We have completed the thread profile of the external metric screw thread M6x1 6g.
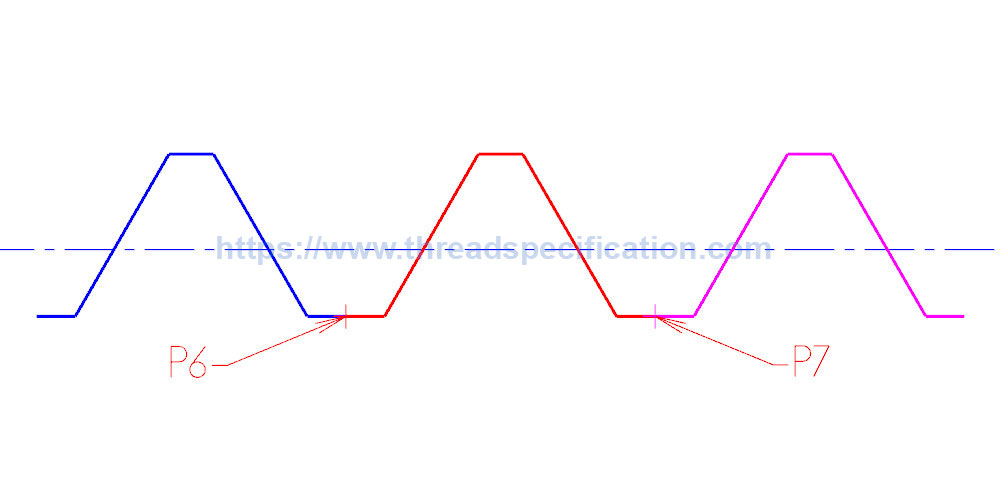
The way to create an internal thread profile is the same as with an external thread. When creating the external thread profile, we create the “thread form” (male or top of thread), but when we create the internal thread profile, we create the “valley form” (female or bottom of thread).