Tapping a hole
Tapping a hole is one of the processes used to create the internal thread by using taps to form the shape of the internal thread. Tapping is an easy, well-known, and highly efficient manufacturing process. This method offers productive and economical threading, especially for smaller threads.
Let’s examine how to tap an internal metric screw thread M6x1 6H effective depth 12mm
Select the drill size to create the hole
The common process for creating the hole is drilling. In this article, we don’t focus on the way to drill the hole; we will discuss how to search for the drill size and calculate the drill depth with the provided effective depth.
Because the hole diameter is the minor diameter of the thread, first of all, we search for the minor diameter of the thread using this website. Go to the Metric Screw Thread (M) page, enter 6 into the size field, 1 for the pitch, select internal, and choose 6H for both pitch and minor diameter tolerance class. After all, we press the search button to get the result.
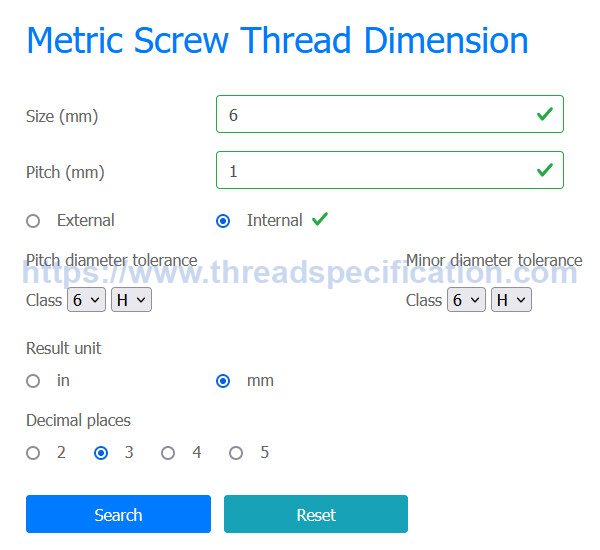
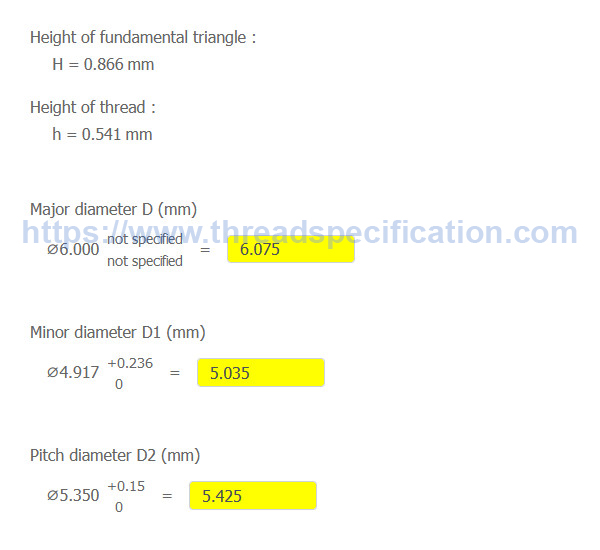
The average value of the minor diameter is 5.035 mm, so we select the nearest value of 5mm for the drill diameter.
Types of taps
The depth of drilling depends on the effective depth of the thread, the type of tap, and the thickness of the material. Assuming that the thickness of the material is thick enough to make the drill hole, we will only focus on the effective depth of the thread and the type of taps.
Depending on the chamfer portion (tapered) at the tip of the tap, we separate into three types of taps for threading: taper tap, plug tap, and bottoming tap.
- Taper taps typically have 8-10 threads that are tapered.
- Plug taps have about 3-5 threads that are tapered.
- A bottoming tap has nearly no taper and a thread count of 1-2.
When processing threads with machinery, plug taps are commonly used for through-hole tapping without using a starter taper tap. If using metalworking machinery, you can start blind hole tapping with a bottoming tap without using a taper and plug tap first.
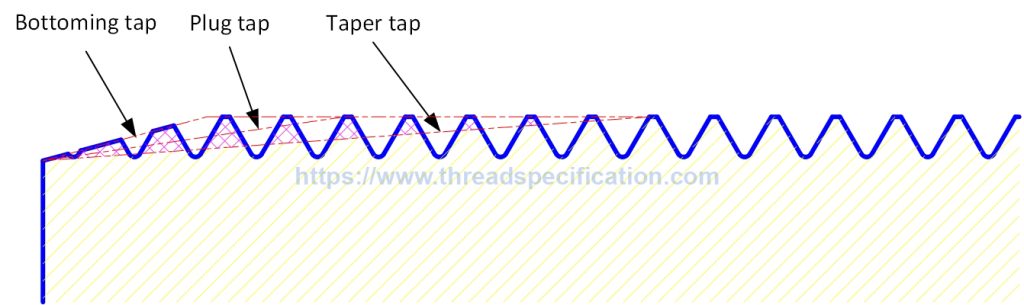
Determine the tap and drill depth
In this example, assume we use the plug tap, so the chamfer portion length is 5 pitches. To make sure we get the effective length, we add 1 pitch for the chamfer portion length, so we use 6 pitches for the chamfer portion.
The chamfer portion length = 6* 1 = 6 mm (1).
The depth of the tapping process is equal to the effective depth plus the chamfer portion length (1):
The depth of tapping = 12 + 6 = 18 mm (2).
For the safety of tapping, we need a clearance of at least 1 pitch for the hole, so the depth of the hole is equal to the depth of tapping (2) plus the clearance.
The hole depth = 18 + 1 = 19 mm (3).
We use the drill to make the hole, so we need to add a small depth equal to the cone height at the tip of the drill. Normally, the tip angle of the drill is 118 degrees, so the height of the cone is:
The height of the cone of drill = drill radius / tan(118°/2) = 3 / 1.6643 = 1.8 mm (4).
So we get the drill depth equal to the hole depth plus the height of the drill cone.
The drill depth = 19 + 1.8 = 20.8 mm (5).
To remove the burr from tapping, we usually add a small chamfer to the hole. The chamfer size can be calculated using this formula:
The chamfer size = (thread size – drill diameter)/2 + clearance.
Assuming we use 0.1 mm for the clearance, the chamfer size becomes:
The chamfer size = (6 – 5)/2 + 0.1 = 0.6 mm (6).
We got the result as shown in the picture below:
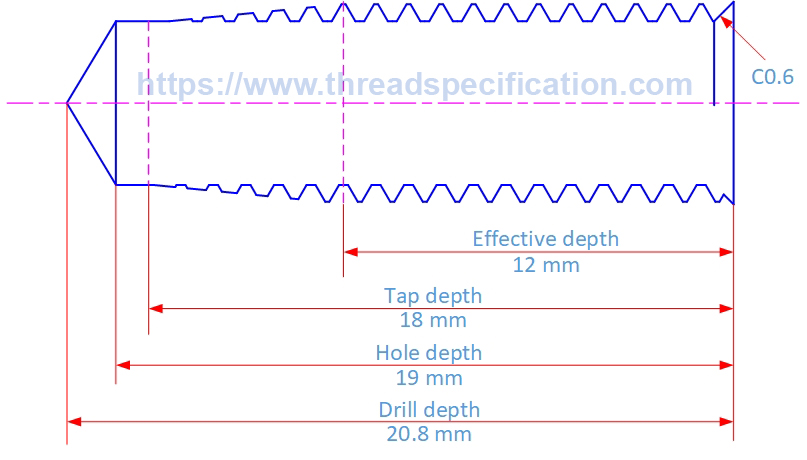